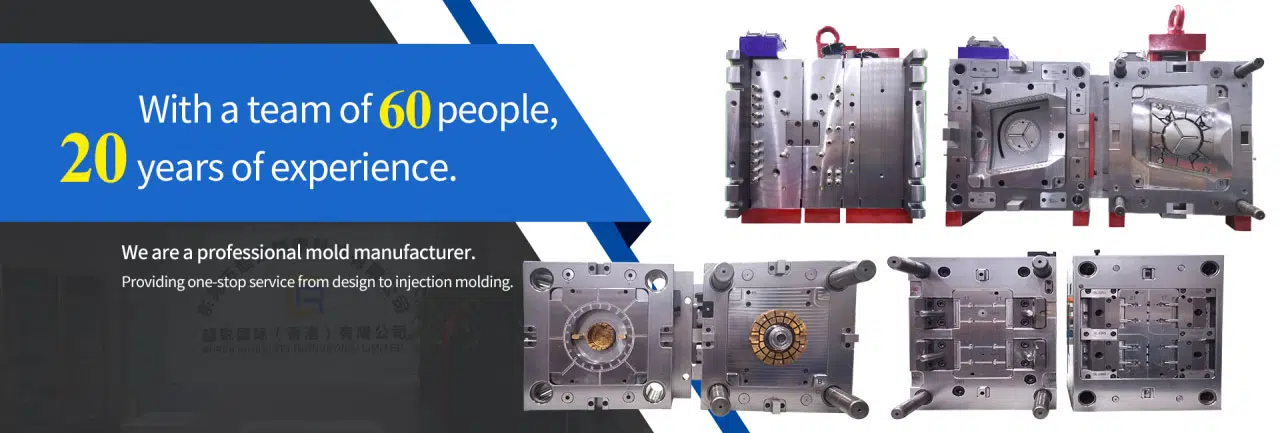
# SKD11 Tool Steel Properties and Applications
## Introduction to SKD11 Tool Steel
SKD11 is a high-carbon, high-chromium tool steel widely used in various industrial applications. This Japanese-grade steel is known for its excellent wear resistance, high hardness, and good dimensional stability after heat treatment. As a cold work tool steel, SKD11 offers superior performance in demanding applications where durability and precision are crucial.
## Chemical Composition of SKD11
The exceptional properties of SKD11 tool steel stem from its carefully balanced chemical composition:
– Carbon (C): 1.40-1.60%
– Chromium (Cr): 11.00-13.00%
– Molybdenum (Mo): 0.80-1.20%
– Vanadium (V): 0.20-0.50%
– Manganese (Mn): ≤0.60%
– Silicon (Si): ≤0.40%
– Phosphorus (P): ≤0.030%
– Sulfur (S): ≤0.030%
This composition provides the steel with its characteristic hardness and wear resistance while maintaining good toughness.
## Mechanical Properties of SKD11
SKD11 tool steel exhibits impressive mechanical properties when properly heat treated:
– Hardness: 58-62 HRC (after heat treatment)
– Tensile Strength: Approximately 2000 MPa
– Yield Strength: Around 1800 MPa
– Elongation: 5-10%
– Impact Toughness: Moderate (varies with heat treatment)
The exact properties can be adjusted through different heat treatment processes to suit specific application requirements.
## Heat Treatment of SKD11
Proper heat treatment is essential to achieve the optimal performance from SKD11 tool steel:
### Annealing
SKD11 is typically supplied in annealed condition with a hardness of about 229 HB. The annealing process involves heating to 800-850°C followed by slow cooling.
### Hardening
For maximum hardness, SKD11 is heated to 1000-1025°C, quenched in oil or air, and then tempered. The quenching process must be carefully controlled to minimize distortion and cracking.
### Tempering
Keyword: SKD11 Tool Steel
After hardening, SKD11 is tempered at 150-200°C to relieve stresses and achieve the desired combination of hardness and toughness. Multiple tempering cycles are often used for best results.
## Applications of SKD11 Tool Steel
SKD11 finds extensive use in various industrial applications due to its excellent properties:
### Tool and Die Making
– Blanking dies
– Forming dies
– Drawing dies
– Cold forging dies
– Thread rolling dies
### Cutting Tools
– Punches
– Shear blades
– Slitter knives
– Cutting blades for paper and plastic
### Precision Components
– Gauges
– Jigs
– Fixtures
– Machine parts requiring high wear resistance
### Plastic Molds
– Injection molds
– Compression molds
– Extrusion dies for plastics
## Advantages of SKD11 Tool Steel
SKD11 offers several benefits that make it a preferred choice for many applications:
– Excellent wear resistance
– High compressive strength
– Good dimensional stability
– Relatively good machinability in annealed condition
– Ability to maintain sharp edges
– Good polishability for mold applications
– Moderate toughness for a high-hardness tool steel
## Machining and Fabrication of SKD11
While SKD11 can be challenging to machine in its hardened state, it’s relatively easy to work with in its annealed condition:
### Machining
– Use carbide tools for best results
– Maintain sharp cutting edges
– Use moderate cutting speeds
– Employ adequate cooling
### Grinding
– Use appropriate grinding wheels (aluminum oxide or CBN)
– Avoid excessive heat buildup
– Use proper coolant application
### EDM Machining
SKD11 responds well to electrical discharge machining, making