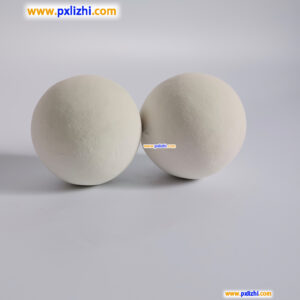
# Inert Ceramic Ball Applications in Industrial Processes
## Introduction to Inert Ceramic Balls
Inert ceramic balls are high-quality, chemically stable ceramic spheres used in various industrial applications. These balls are manufactured from high-purity materials like alumina, zirconia, or silica, offering excellent resistance to thermal shock, chemical corrosion, and mechanical wear.
## Key Properties of Inert Ceramic Balls
The effectiveness of inert ceramic balls in industrial processes stems from their unique properties:
- High temperature resistance (up to 1800°C)
- Excellent chemical inertness
- Superior mechanical strength
- Low thermal expansion coefficient
- Resistance to thermal shock
- Uniform size distribution
## Major Industrial Applications
1. Catalyst Support in Petrochemical Industry
Inert ceramic balls serve as excellent catalyst supports in petroleum refining and petrochemical processes. They provide structural support to catalysts while ensuring proper gas distribution through packed beds.
2. Tower Packing in Chemical Processing
These ceramic balls are widely used as tower packing materials in distillation, absorption, and stripping columns. Their inert nature prevents contamination of processed chemicals while maintaining efficient mass transfer.
3. Grinding Media in Ball Mills
Due to their high density and wear resistance, inert ceramic balls are ideal grinding media for ball mills in mineral processing, paint manufacturing, and ceramic powder production.
4. Heat Exchange Media
In high-temperature heat exchange systems, ceramic balls serve as heat storage and transfer media, particularly in regenerative heat exchangers and thermal storage applications.
5. Gas Distribution in Industrial Furnaces
Ceramic balls are used to create uniform gas distribution layers in industrial furnaces and reformers, ensuring even heat distribution and process efficiency.
## Advantages Over Alternative Materials
Compared to metal or plastic alternatives, inert ceramic balls offer:
- Longer service life in harsh environments
- Lower maintenance requirements
- Better resistance to chemical attack
- Higher temperature tolerance
- Reduced contamination risks
Keyword: inert ceramic ball
## Selection Considerations
Size and Density
The appropriate size and density of ceramic balls should be selected based on the specific process requirements, considering factors like flow rates and pressure drops.
Material Composition
Different alumina content (92%, 95%, or 99%) offers varying levels of chemical resistance and mechanical strength for different applications.
Surface Characteristics
Smooth surfaces reduce friction and abrasion, while slightly textured surfaces may enhance certain catalytic applications.
## Maintenance and Handling
While inert ceramic balls are durable, proper handling is essential:
- Store in dry conditions to prevent moisture absorption
- Handle carefully to avoid chipping or cracking
- Regularly inspect for signs of wear or contamination
- Follow manufacturer’s guidelines for cleaning and regeneration
## Future Trends in Ceramic Ball Technology
Emerging developments include:
- Nanostructured ceramic balls for enhanced performance
- Smart ceramic balls with embedded sensors
- Eco-friendly manufacturing processes
- Custom-designed shapes for specialized applications
## Conclusion
Inert ceramic balls play a vital role in numerous industrial processes, offering unmatched performance in harsh operating conditions. Their versatility, durability, and chemical stability make them indispensable in industries ranging from petrochemicals to environmental protection. As technology advances