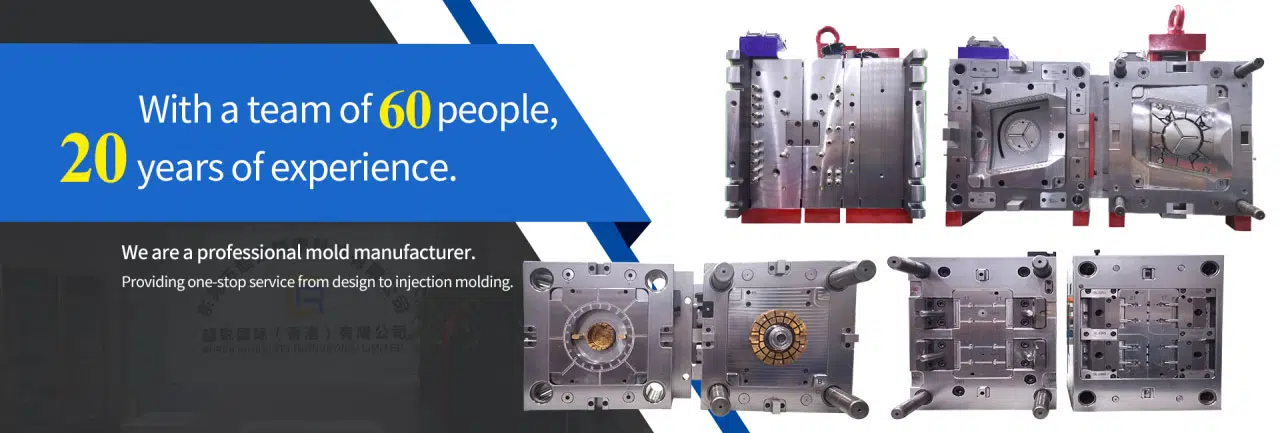
# Die Casting Process Optimization Techniques
## Introduction to Die Casting Optimization
Die casting is a highly efficient manufacturing process that produces precise metal parts with excellent surface finishes. However, to maximize productivity and minimize costs, manufacturers must continually optimize their die casting processes. This article explores several key techniques for improving die casting operations.
## Key Optimization Areas
### 1. Mold Design Improvements
Optimizing mold design is crucial for efficient die casting. Consider these approaches:
- Implement conformal cooling channels to improve heat transfer
- Use simulation software to predict and prevent potential defects
- Optimize gate and runner systems for better metal flow
- Select appropriate mold materials for specific applications
### 2. Process Parameter Optimization
Fine-tuning process parameters can significantly impact quality and efficiency:
- Adjust injection speeds based on part geometry
- Optimize melt temperature for the specific alloy being used
- Control die temperature to prevent premature solidification
- Determine optimal lubrication cycles
### 3. Material Selection and Handling
Alloy Considerations
Choosing the right alloy affects both process efficiency and final part quality:
- Evaluate mechanical property requirements
- Consider thermal characteristics
- Assess corrosion resistance needs
Material Preparation
Proper material handling improves consistency:
- Implement strict melt quality control
- Use degassing techniques when necessary
- Maintain proper holding furnace temperatures
## Advanced Optimization Techniques
### 1. Real-Time Monitoring Systems
Implementing sensors and monitoring systems allows for:
- Continuous process parameter tracking
- Early detection of potential issues
- Data collection for predictive maintenance
### 2. Automation Integration
Automation can significantly improve die casting operations:
- Robotic part extraction and handling
- Automated lubrication systems
- Computer-controlled process adjustments
### 3. Energy Efficiency Measures
Reducing energy consumption lowers costs and environmental impact:
- Implement heat recovery systems
- Optimize machine cycle times
- Use energy-efficient melting equipment
## Continuous Improvement Approach
Successful die casting optimization requires an ongoing commitment:
- Regularly analyze production data
- Implement lean manufacturing principles
- Train operators on best practices
- Stay updated on new technologies
Keyword: Die Casting
By systematically applying these optimization techniques, die casting operations can achieve higher quality, greater efficiency, and improved profitability.