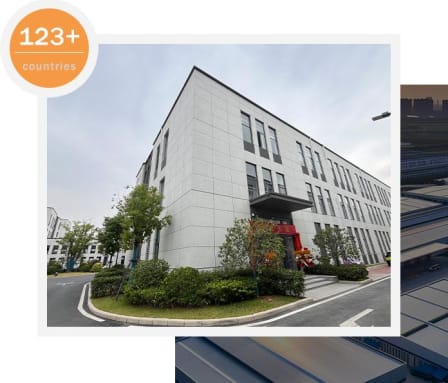
,字数在1000字左右
html
PDC Bit with OEM Shaped Cutter for Enhanced Drilling Performance
In the ever-evolving world of drilling technology, the demand for high-performance tools that can withstand extreme conditions while delivering superior results is at an all-time high. One such innovation that has revolutionized the industry is the PDC bit with OEM shaped cutter. This advanced tool combines the durability of polycrystalline diamond compact (PDC) cutters with custom-engineered shapes to optimize drilling efficiency and longevity.
Understanding PDC Bits and Their Importance
PDC bits are widely used in oil, gas, and mining drilling operations due to their exceptional hardness and wear resistance. These bits feature synthetic diamond cutters bonded to a tungsten carbide substrate, making them ideal for penetrating hard and abrasive formations. However, not all PDC bits are created equal. The introduction of OEM shaped cutters has taken their performance to new heights.
The Role of OEM Shaped Cutters in PDC Bits
OEM (Original Equipment Manufacturer) shaped cutters are custom-designed to meet specific drilling challenges. Unlike standard cutters, these are precision-engineered with unique geometries to enhance cutting efficiency, reduce heat buildup, and minimize wear. Some common shapes include:
- Chamfered Edge Cutters – Reduce stress concentrations and improve impact resistance.
- Concave Cutters – Enhance rock shearing efficiency and reduce friction.
- Asymmetric Cutters – Optimize directional drilling performance.
Benefits of Using PDC Bits with OEM Shaped Cutters
The integration of OEM shaped cutters into PDC bits offers several advantages:
1. Improved Drilling Speed
Custom-shaped cutters allow for more efficient rock removal, reducing the time required to drill through tough formations. This leads to faster project completion and lower operational costs.
2. Extended Bit Life
The specialized geometries of OEM cutters distribute wear more evenly, significantly increasing the lifespan of the bit compared to conventional designs.
3. Enhanced Stability and Control
Shaped cutters help maintain bit stability, reducing vibrations and improving directional control—especially crucial in complex drilling environments.
4. Reduced Energy Consumption
By minimizing friction and optimizing cutting efficiency, these bits require less torque and energy, contributing to more sustainable drilling operations.
Applications of PDC Bits with OEM Shaped Cutters
These advanced bits are particularly effective in:
- Oil and Gas Exploration – Ideal for drilling through hard shale, sandstone, and limestone formations.
- Geothermal Drilling – Withstands high temperatures and abrasive rock conditions.
- Mining Operations – Enhances penetration rates in mineral extraction.
Keyword: oem shaped cutter pdc bit
Choosing the Right PDC Bit with OEM Shaped Cutters
Selecting the optimal bit depends on several factors:
- Formation Type – Different cutter shapes perform better in specific rock types.
- Drilling Parameters – Weight on bit (WOB), rotation speed (RPM), and hydraulics must be considered.
- Bit Design – Blade count, cutter layout, and