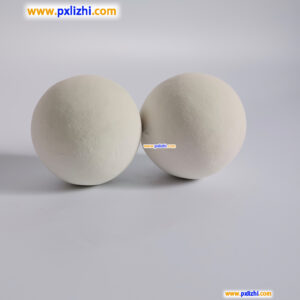
# Inert Ceramic Balls: Essential Components for Industrial Applications
## What Are Inert Ceramic Balls?
Inert ceramic balls are high-performance ceramic spheres designed for use in various industrial processes. These balls are made from high-quality, chemically inert materials that resist corrosion and maintain structural integrity under extreme conditions. Their primary function is to serve as support media, catalysts, or packing materials in chemical reactors, distillation columns, and other industrial equipment.
## Key Properties of Inert Ceramic Balls
The effectiveness of inert ceramic balls in industrial applications stems from their unique combination of properties:
– High temperature resistance (up to 1600°C)
– Excellent chemical stability
– Superior mechanical strength
– Low thermal expansion coefficient
– Resistance to thermal shock
– Smooth surface finish
– Uniform size distribution
## Common Applications in Industry
### 1. Catalyst Support in Petrochemical Industry
Inert ceramic balls serve as excellent catalyst supports in petroleum refining and petrochemical processing. They provide a stable base for active catalysts while ensuring proper gas or liquid distribution throughout the reactor.
### 2. Packing Material in Distillation Columns
These ceramic balls are widely used as tower packing in distillation and absorption columns. Their spherical shape promotes efficient mass transfer while minimizing pressure drop across the column.
### 3. Heat Exchange Media
Due to their thermal stability, inert ceramic balls function effectively as heat exchange media in high-temperature processes, transferring heat while resisting chemical attack.
### 4. Grinding Media
Keyword: inert ceramic ball
In certain applications, these ceramic balls serve as grinding media in ball mills, particularly when processing materials that require contamination-free environments.
## Manufacturing Process
The production of high-quality inert ceramic balls involves several critical steps:
1. Raw material selection (typically alumina, zirconia, or silicon carbide)
2. Precise mixing and formulation
3. Forming through isostatic pressing or extrusion
4. High-temperature sintering
5. Precision grinding and polishing
6. Strict quality control testing
## Advantages Over Alternative Materials
Inert ceramic balls offer significant benefits compared to metal or plastic alternatives:
– Longer service life in corrosive environments
– Better performance at extreme temperatures
– Lower maintenance requirements
– Reduced contamination risk
– More consistent performance over time
## Selection Considerations
When choosing inert ceramic balls for specific applications, engineers should consider:
– Operating temperature range
– Chemical environment
– Required mechanical strength
– Size specifications
– Surface characteristics
– Cost-effectiveness for the application
## Future Developments
The inert ceramic ball industry continues to evolve with advancements in material science. Researchers are developing new ceramic formulations with enhanced properties, including:
– Higher porosity for improved catalytic performance
– Increased fracture toughness
– Better resistance to specific chemical attacks
– More precise size control for specialized applications
As industrial processes become more demanding, inert ceramic balls will remain essential components, offering reliable performance in challenging environments across multiple sectors.