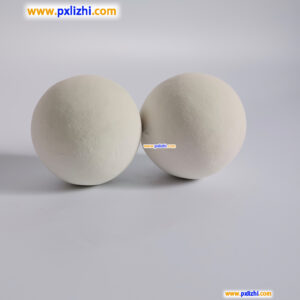
# Inert Ceramic Ball Applications in Industrial Processes
## Introduction to Inert Ceramic Balls
Inert ceramic balls are widely used in various industrial processes due to their excellent chemical stability, high temperature resistance, and mechanical strength. These small spherical ceramic components play a crucial role in many chemical and petrochemical applications, serving as catalyst supports, tower packing, and bed support media.
## Key Properties of Inert Ceramic Balls
Keyword: inert ceramic ball
The effectiveness of inert ceramic balls in industrial applications stems from their unique properties:
– High chemical inertness
– Excellent thermal stability
– Superior mechanical strength
– Low water absorption
– Resistance to corrosion and abrasion
## Major Industrial Applications
### 1. Catalyst Support in Chemical Reactors
Inert ceramic balls are extensively used as catalyst supports in fixed-bed reactors. They provide a stable foundation for active catalysts while ensuring proper gas or liquid distribution throughout the reactor bed. Their thermal stability makes them ideal for high-temperature catalytic processes.
### 2. Tower Packing in Distillation Columns
These ceramic balls serve as efficient packing materials in distillation and absorption towers. Their spherical shape promotes excellent vapor-liquid contact while minimizing pressure drop across the column. This application is particularly valuable in petroleum refining and gas processing plants.
### 3. Bed Support in Filtration Systems
In water treatment and other filtration processes, inert ceramic balls are used as support media for filter beds. They prevent the loss of finer filtration materials while maintaining proper flow distribution through the system.
### 4. Thermal Insulation in High-Temperature Processes
Due to their excellent thermal properties, inert ceramic balls are employed as insulating materials in various high-temperature industrial processes, including furnace operations and heat treatment applications.
## Advantages Over Alternative Materials
When compared to metal or plastic alternatives, inert ceramic balls offer several distinct advantages:
– Longer service life in corrosive environments
– Better performance at extreme temperatures
– Lower maintenance requirements
– More consistent performance over time
– Reduced risk of contamination in sensitive processes
## Selection Considerations
When choosing inert ceramic balls for industrial applications, several factors should be considered:
– Operating temperature range
– Chemical environment
– Required mechanical strength
– Size and density specifications
– Pressure drop requirements
– Cost-effectiveness for the specific application
## Future Trends in Inert Ceramic Ball Applications
As industrial processes become more sophisticated, the demand for high-performance inert ceramic balls continues to grow. Recent developments include:
– Advanced ceramic formulations for extreme conditions
– Customized shapes for specific flow dynamics
– Improved manufacturing techniques for greater consistency
– Environmentally friendly production methods
With their unique combination of properties, inert ceramic balls will remain essential components in numerous industrial processes for years to come.